Leak Test Reduces Waste and Optimizes the Production
New Zealand New Milk Ltd. produces predominantly milk powder for babies. When working with nutritional products it is very important to make sure that all products meet the required standards. When people trust you with the health and growth of their babies you feel even more obliged to make sure your product is first-rate. This is exactly the case for New Zealand’s NewMilkTM.
New Zealand New Milk Ltd. buys dairy powders from other producers in New Zealand and Australia and turns it into a nutritional formula for babies. They supply the dairy-based nutritional powders in sealed cans and single-serve sachets and sell it primarily to the Asian and Australian market. NewMilkTM benefits from a very good reputation in the market, and the products are positioned as high-end.
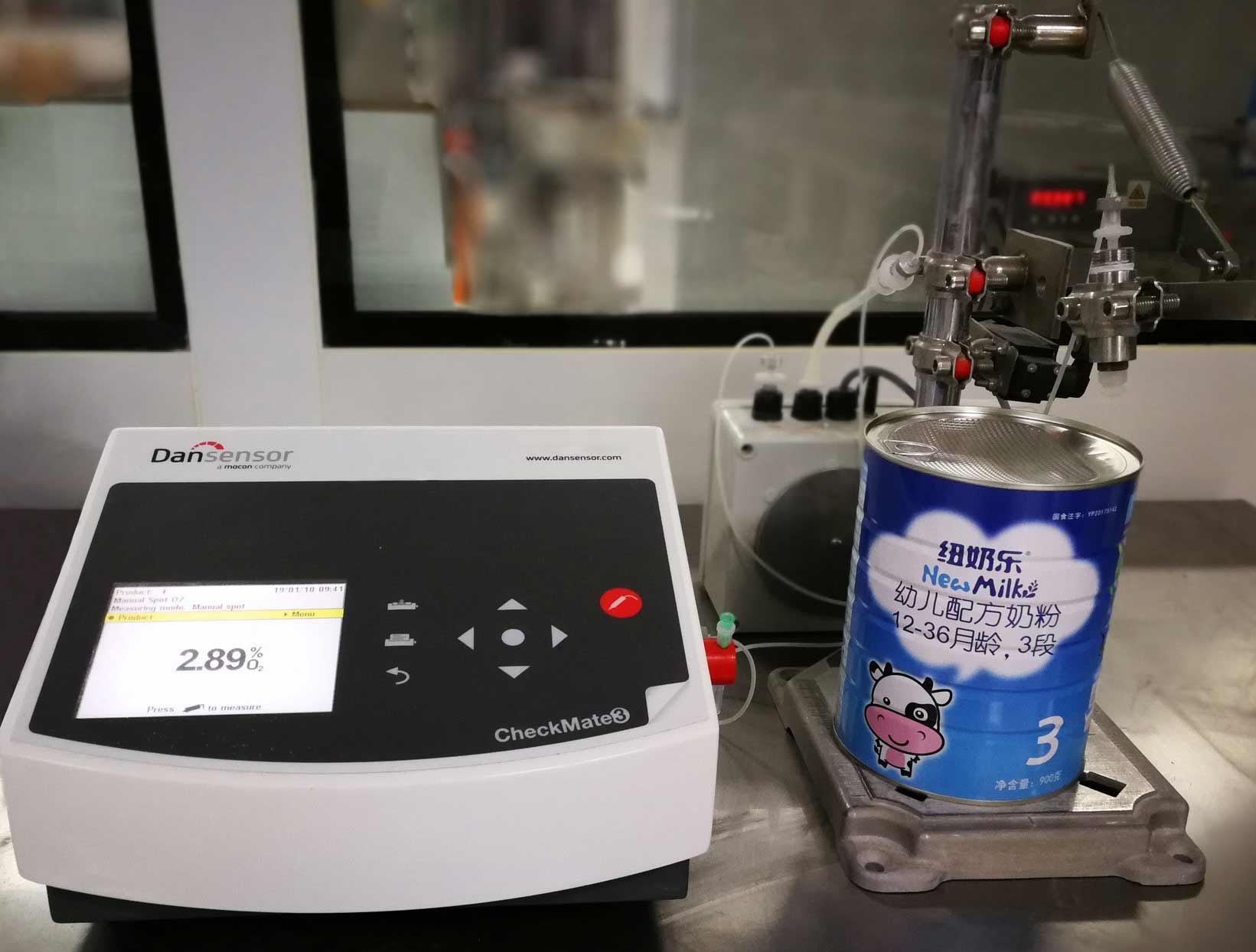 |
“In order to maintain this reputation we are very stringent with our production and test methods. We have two production facilities, both with highly automated equipment and video surveillance of the entire production line. We always make sure to use state of the art technology, so we can keep up with national quality standards of all the markets we supply,” says Silvana Foerster, Technical Manager at New Zealand New Milk. “
|
We have never had any customer complaints for leaking cans and we certainly do not want to get any. When we first began using MAP in 2015 we moved proactively because we wanted to improve the production process and the quality of our products. We then invested in two Dansensor MAP Check 3 gas analyzers – one for each production facility and three
Dansensor MAP Mix Provectus gas mixers”.

Saving of approx. 2,000 cans per week
When using MAP in the packaging process it is necessary to make sure all packages are 100 percent airtight. Even the tiniest leak will destroy the MAP effect, and the product will not last until the promised expiry date of up to 24 months. Furthermore, the soft foil lid will bulge as a sign of a leak.
“At New Milk’s two production facilities we test 14 cans every 30 minutes, 12 hours per day, 6 days per week, which in total is 2,016 cans per week. Before we acquired our latest testing equipment from MOCON Europe – two Dansensor LeakPointer II and two Dansensor CheckMate 3, we tested the packages in a pressurized water bath. When you do the testing in water you have to discard the samples afterwards because you risk bacteria growth on the outside of the can from remaining water and eventually rust will develop also. The Dansensor LeakPointer II enabled us to increase testing frequency as operators are less occupied afterwards with disposal of tested cans. Further to this the leak test can be performed in the critical hygiene area, where the filling takes place, and samples for testing do not need to be transferred to the outer area. This means less handling and increased efficiency on the line. Multiply 2,000 cans by the average price per can of $10 it is easy to see that we save a lot of money by using the dry-testing method (trace gas leak test) and not having to discard the tested packages,” Silvana explains.
Always great support
When Bob Olayo, Manager at mätt solution (formerly FF Instrumentation Ltd.) and distributor of MOCON Europe equipment in New Zealand, first introduced the Dansensor LeakPointer II and the dry testing method (trace gas leak test) Silvana and her team were quick to do the math and found out that this method would be advantageous to their business. Not only would they save a lot of money on reducing waste, they would also be able to test all the products.
“Of course, buying new equipment means a big investment to the company. We chose MOCON Europe products because they represent the best money can buy and we always get reliable advice and support from Bob at mätt solution.
Although mätt solution is situated many miles away, Bob is always willing to help whenever we call him. If it is not possible to solve the problem over the phone he is happy to travel all the way from Christchurch to Auckland - a distance of over 1,200 kilometers,” Silvana says. When New Zealand New Milk opened their second production facility two years ago they chose to implement exactly the same packaging line as in the existing production facility. “The MOCON Europe equipment really has helped us a lot, so why not continue using it in our new facility? MOCON Europe’s excellent world-wide reputation of their equipment gives us as well as our auditors and customers confidence,” Silvana says.