-
Home
-
-
Blogposts
-
-
9 Tips to Choose the Best Packaging Material for Modified Atmosphere Packaging
-
9 Tips to Choose the Best Packaging Material for Modified Atmosphere Packaging
Shelf life down: leak or permeation?
You’ve just spent tens of thousands of dollars developing a revolutionary new nutrition supplement for the sports market. You’ve decided on the type of packaging – a polymer film that is turned into pouches and heat-sealed. You have determined that the best way to keep the fresh and extend the shelf life is to use Modified Atmosphere Packaging (MAP).
So on the packaging lines you flush the bags with nitrogen to displace the air and thereby remove oxygen. You ship the products. So far, so good. But then you start getting reports that the product on the shelf is going ‘off’ well before the use-by date.
You test the bags for leaks, but you can’t find any. Something is going wrong, but what?
Permeation
The answer could well be a phenomenon called permeation. Even though the packages are sealed and leak-free, oxygen from the air is seeping through the polymer film and into the package.
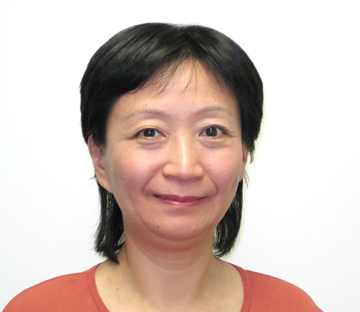
Georgia Gu
Senior Scientist
MOCON Inc. |
You have chosen the wrong sort of packaging material for your product.
Georgia Gu is a Senior Scientist for the packaging instrumentation specialist MOCON Inc. and is an expert in permeation. Here, Georgia explains the importance of permeation in MAP. |
Polymers are permeable!
“Traditional packaging materials such as glass or metal are impermeable – gases cannot pass through them,” says Georgia. “Modern polymers on the other hand are permeable”.
This means that over time molecules in the surrounding air such as oxygen or water vapour can slowly seep through and into the package. If you are using MAP and the packaging material is permeable to the gas you are trying to keep out, then your MAP will not be effective.
There are many different polymer packaging materials on the market that have different permeability properties. Some are effective barriers to oxygen, some to water vapour.
The thickness of the film also affects permeation. “Double the thickness of the film and you will halve the transmission rate,” explains Georgia. “But beware of ‘over-engineering’ your packaging to well beyond what is needed. This could increase costs needlessly”.
Nine ways to ensure you get the best barrier material for your MAP product
Here are Georgia’s top tips for ensuring that you select the right packaging for your product.
- You need to know your product! What is it susceptible to? Do you need to keep oxygen out, or is it more sensitive to moisture? For example food products that contain fats are often sensitive to oxygen, which promotes off odor due to oxidation, or the growth of microbes that spoil the food. Pharmaceutical products are often sensitive to moisture. You need to do proper lab tests to find out what your product is most sensitive to. When you know the answer to this question you are then able start to identify the best material with the right barrier properties.
- There are instruments that can test the barrier properties of polymer materials. These instruments can measure the oxygen transmission rate (OTR) or water vapour transmission rate (WVTR). You can buy these instruments to carry out tests in-house, or you can contract the testing to a specialist company to do it for you.
- Be aware that the environment can affect permeation and therefore shelf life. If you do all your tests under ‘normal conditions’ but then export your product to, say, a tropical country you might have problems. A 10 degree increase in temperature will double the permeation rate. Humidity also affects permeation. So if you export to a hot, humid country be aware of these issues. Know your market!
- Be wary of simply opting for a packaging material because it ‘should be ok’, or because your competitor uses it. They might have different product ingredients or packaging processes to yours, or indeed they might not have got their material right. Do your own tests.
Here is a real-life example. A manufacturer of nutrition powder was using MAP to flush their packages with nitrogen to eliminate ambient oxygen and moisture. For the packaging material they used a polymer called HDPE. But the powder was spoiling after only a relatively short period. After taking advice they switched to a polymer called PET and the problem was solved. Why? Because while HDPE is a good moisture barrier, it is a poor barrier to oxygen. PET on the other hand is a much better oxygen barrier.
- Don’t forget the importance of testing for leaks. If your MAP product is losing shelf life it could be that the packages are leaking. There are very good instruments on the market for leak testing. These can be integrated into the packaging line, so that each package is tested individually. Or you can get ‘off-line’ leak detectors, allowing you to test packages randomly. The best tests are non-destructive, so that you do not waste product or packaging materials. Read more about non-destructive testing technology.
- If you cannot find any leaks but the product is still losing shelf life, then there could be an issue with permeation.
- Bear in mind that different batches of packaging material can vary if the supplier is not carrying out proper quality control. So while one batch of material might have good barrier properties another one might not. Testing is a good idea. Read a case study about quality control.
- It is costly to invest in a packaging plant and to get a production underway only to find that the shelf life is poor because you have not thought carefully enough about your packaging material and its permeability properties. It is a good idea to consult with specialists too and carry out investigations so that you choose the best packaging material for you product.
- Finally: remember that it is crucial to make sure your packages have the right gas composition. So remember to check the residual O2 level.