-
Home
-
-
Blogposts
-
-
LEANER AND GREENER: Avoid the Waste of Manual Testing in MAP
-
LEANER AND GREENER: Avoid the Waste of Manual Testing in MAP
At MOCON Europe (Dansensor) we spend a lot of time visiting food processing companies around the world to offer advice on where they can reduce costs and get more for their buck. That’s actually what one of our main objectives is – helping our clients who use Modified Atmosphere Packaging (MAP) to achieve the most efficient and cost effective quality assurance possible. Read about the history of MAP in this blogpost.
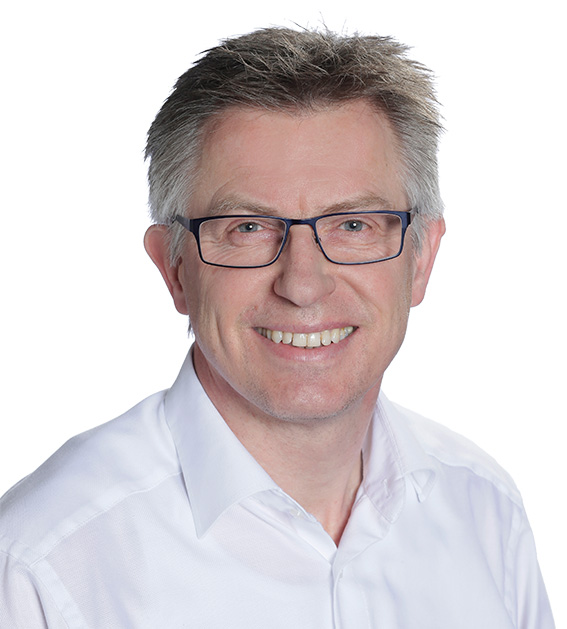 |
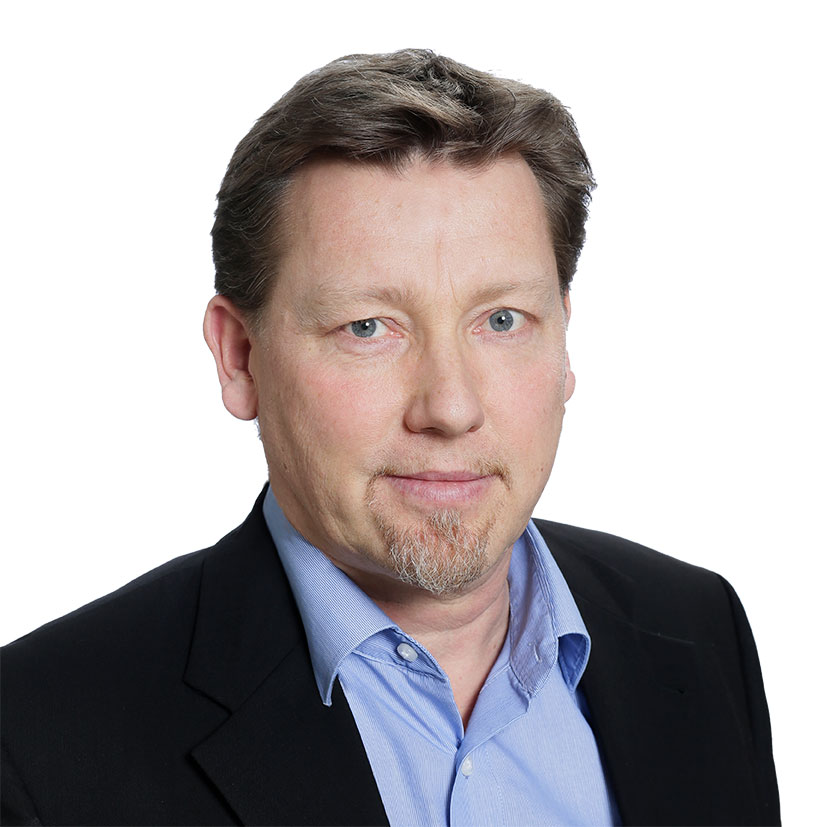 |
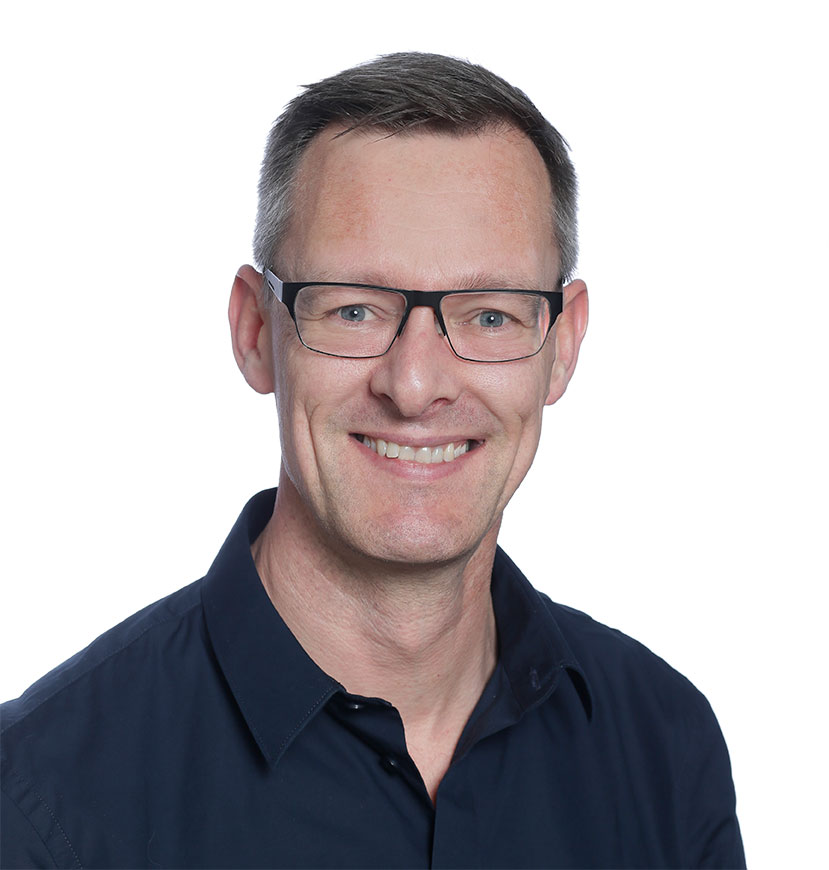 |
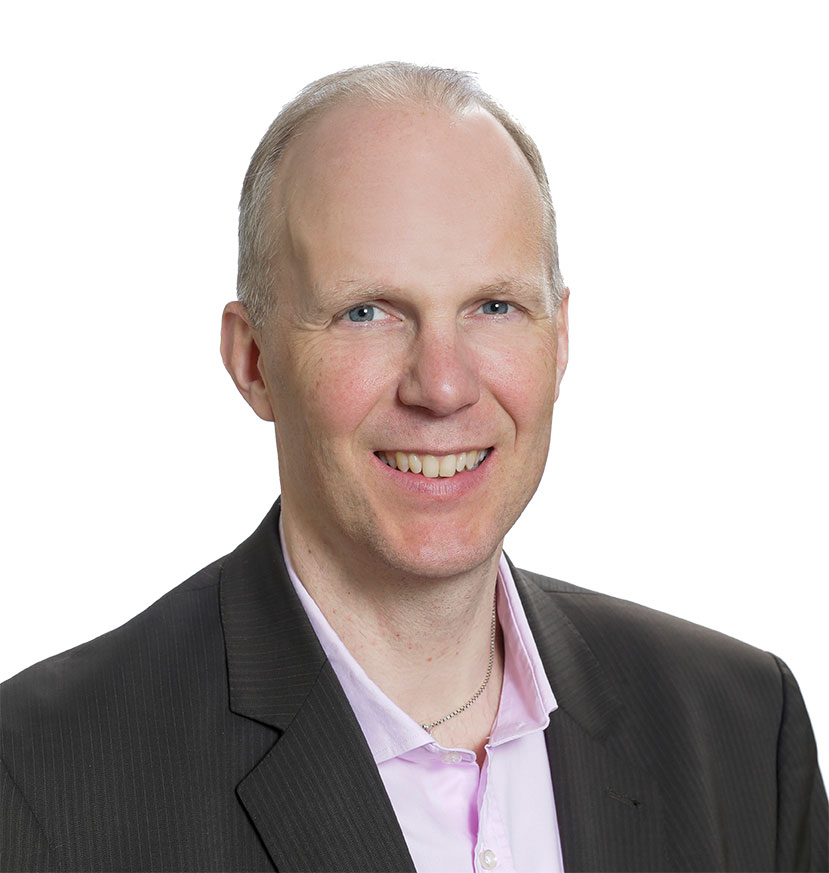 |
Steen Andreasen
Product Manager
MOCON Europe A/S |
Tony Johansen
Area Sales Manager
MOCON Europe A/S |
Morten Torngaard
Sales Manager
MOCON Europe A/S |
Steen Andersen
OEM Manager
MOCON Europe A/S |
For MAP, one crucial aspect of quality assurance is to ensure that the gas mixture within the package is correct. If the mixture deviates from the required limits this can result in a reduced shelf life of the product with the potential for costly returns from the retailer . Let us share some of the great insights that have saved other companies a lot of money…
Manual testing produces more waste than you might realise!
Many companies use manual testing to check the headspace gas of the packages coming off the line. Typically the quality assurance operator will remove a package at regular intervals, every 15 minutes say, and measure the headspace gas by puncturing the packaging with a needle, which draws a sample of the headspace gas into the test instrument.
For a relatively small company that processes only low volumes of product this is perfectly adequate. But for larger volume manufactures the waste that such a regime generates can be startling.
Consider this. You are a company running two MAP lines which produce packets of cheese, for example. Every 15 minutes you take one package from each machine to test the headspace gas mixture. For the two lines that is 8 packages each hour. Sounds not too bad. But for two 8-hour shifts a day, that means 128 packages are tested. If your lines are running for 300 days a year that equates to an eye-watering 38,400 packages each year.
|
Remember, each time you test a sample you are puncturing the packaging. This has two consequences straight off: you must repackage that particular sample, and you must discard the original packaging. Furthermore, all this takes time. Someone has to carry out these tests, and more often than not log the results by hand, and then file them and store them in a folder or some such. Also, if the person does find a problem with one of the packages, then he or she has to turn detective to find out how many packages were affected since the last test 15 minutes earlier – 10 minutes’ worth, 5 minutes’ worth? This means more packages must be tested: more waste packaging, more re-packaging and more time.
And that is just for two lines; many companies might be running six or eight such lines. This system results in waste at many, many levels: you produce a small mountain of waste packaging material, which has a cost, you must repackage the tested samples, which effectively reduces the capacity of your line, and you must pay for the extra labour costs of the testing regime.
Control the MAP process automatically
Fortunately there is a relatively simple solution to this. Over recent years the food industry has been moving increasingly towards what is termed ‘process control’, with more automated control systems and fewer people in the production area. This trend has accelerated as packaging machines have become ever faster.
By making a process control setup an integral part of the production line which ensures that the correct mixture is flushed into the packages before they are sealed, you can eliminate a lot of the waste from manual control. So, for instance if the gas mixture falls outside your pre-set limits, the process control setup automatically shuts down the line so that no packages are given the wrong mixture.
This is a really nice example of process control: rather than identifying a problem after it has already happened, as is the case with manual testing, you are preventing the problem from arising in the first place. You can read about process control in this
case study.
Savings at every level
This approach gives you savings at virtually every level: you destroy fewer packages so you generate much less waste; you reprocess fewer packages so you increase your productivity; and you need much less manpower so you reduce labour costs.
By using a process control setup you can enable the exact right amount of gas for flushing. Manual processes often are too cautious (that’s good), but this means they use an excess of flushing gas, CO
2 say, which is also wasteful. So by taking out the manual control, you get a substantial savings on your gas bill. And of course all this means that you boost your environmental credentials because you are running a much greener operation.
And this process control approach has other advantages too, not least the fact that the system automatically and constantly logs relevant data, on things such as the gas mixture. This means there is no need for someone to write down this information on a piece of paper and file it away. It also makes things a lot easier for auditing purposes or demonstrating to your client the robustness of your quality assurance systems.
A cost-effective solution
It is pretty straightforward to make a business case for investing in a process control setup as the savings invariably justify the investment. You don’t have to just take my word for it. We have several case studies where our clients changed from our handheld products to our process control products and services such as the Dansensor
® MAP Check 3.
For instance KiMs, one of Scandinavia’s leading producers of crisps, nuts and snack foods, reckoned that they would recoup the cost of their investment in the process control system within a year – after that it is all savings. You can read about it in this
case study.