-
Home
-
-
Blogposts
-
-
CREEP, BUBBLE AND BURST... Ensuring Package Seal Integrity for Medical and Healthcare Products
-
CREEP, BUBBLE AND BURST... Ensuring Package Seal Integrity for Medical and Healthcare Products
Peter Schlösser is former Product Manager for the healthcare market in Europe for MOCON, Dansensor’s parent company. Peter is now Service Manager in MOCON GmbH Germany. Peter, who has a background in both electrical engineering and economics, has many years’ experience in package testing technology. Here Peter gives some thoughts on the importance of a robust package-testing regime for companies who package medical and healthcare products.
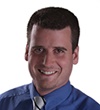 |
Peter Schlösser
Service Manager
MOCON GmbH. |
A matter of life and death: Seal integrity
The way that medical products and devices are packaged and sealed is vital. In fact I don’t think it is an exaggeration to say that it can, literally, be a matter of life and death. That is why regulators around the world apply strict standards to the methods used to package devices and to the testing regimes to ensure that the packaging is properly sealed and that the seal will remain intact while the product is transported and stored. Many countries for example adopt the universally accepted standards devised by ASTM International (formerly the American Society for Testing and Materials).
This is because anything that is to be placed within the human body – from a needle on a syringe to a pacemaker or other implanted device – must be free from contaminants. These include such things as bacteria that could cause serious and potentially fatal harm if they were carried into the patient on a medical device.
Manufacturers use a range of methods to sterilize devices during the packaging process to ensure they are free from contamination. Once the package is sealed it is crucial that there are no leaks and that the seal remains intact until the device is removed and used. If, for example, a surgeon discovered that the packaging on a pacemaker was faulty, the device would need to be discarded and all the pacemakers in that batch would almost certainly have to be recalled by the manufacturer. And product recalls are a manufacturer’s worst nightmare. They cause huge expense and can seriously damage the company’s reputation. Read more about
Leak detection.
Combined medicines and devices
Over recent years there has been an interesting development in the way that medical products are presented, and this has an important bearing on packaging. In the past you would have a package containing a syringe and needle which would be supplied by a specialist medical devices company. You would also have a separate glass vial with a rubber seal containing the drug, supplied by the pharmaceutical company. The doctor or nurse would pierce the seal with the needle and draw the drug into the syringe before injecting it into the patient.
But now there is a strong move towards pre-filled syringes: the syringe already loaded with the drug is sealed in a sterile package. This is a significant shift. In the past it was straightforward to sterilize a glass vial, put the medicine in and seal it. A simple process with no big issues of seal integrity or leakage.
But now things are more complicated. The medicine and the device are contained within one package and this introduces new challenges in the pharmaceutical industry for sterility and seal integrity. This is a relatively new development and many pharma people have little experience with the regulations and technical requirements. I think this is an important emerging market for package testing.
Robust and validated testing
So we need robust and validated methods to test the integrity of packaging. The way that we work with this is straightforward. When using a package testing device, you place an adhesive polymer seal on the package and then pierce the package through the seal with a hollow needle. The package is then inflated at a precisely controlled and closely monitored pressure. The adhesive seal prevents any leakage when air is pumped into the package. The operator can then carry out a range of different tests – all validated and accepted by the regulatory authorities – depending on what is being investigated. Read a case study about
leak and seal strength.
The Bubble test
To test for leaks, for example, the operator would place the package under water; as the pressure increases any leak will be revealed by bubbles in the water. Perhaps not surprisingly this is called a bubble test. A validated bubble test will comply with ASTM F2096.
Or there is the burst test. Here you pressurize the package until the seal bursts. This provides key information about the bond strength of the package seal, or the strength of the packaging material. This should comply with ASTM F2054.
Another test is called the creep or peel test. Here the package is placed under a constant pressure for a set amount of time to see if the seal peels (ASTM F1140).
An alternative way for testing for leaks apart from the bubble test is to apply a constant pressure over a period of time to see if any pressure is lost – which would indicate a leak (ASTM F2095). In fact this test can even be used to calculate the size of the hole which forms the leak.
Further information about
ASTM standards.
Learning lessons from food packaging
My final thought. The food sector has had many decades’ experience of developing robust package-testing technologies to ensure seal integrity. This is so that food products stay fresh for longer and have an extended shelf-life. Many of the challenges faced by the medical devices sector in terms of packaging are pretty much that same as those that have been successfully tackled by the food industry. So there is good scope for cross-fertilization here and the medical devices people can learn a lot from the testing systems used in the food arena. Read about a
consumer survey conducted by Dansensor in this blogpost.