-
Home
-
-
Blogposts
-
-
Fit to Burst: Quality Assurance in Package Sealing
-
Fit to Burst: Quality Assurance in Package Sealing
Too loose or too tight?
So you’ve had a hard day’s work and you are settling down before dinner in front of the TV with a packet of potato chips. You take each side of the bag between thumb and forefinger and pull gently, expecting the top of the bag to smoothly peel apart. But it doesn’t. So you pull harder. And harder. Then it suddenly splits open and you are showered by the contents. The bag was sealed too tightly and your evening has not got off to a great start.
Or maybe the bag opens just a bit too easily. And when you try one of the chips it is stale. The reason for this – although you do not know it – is that the consignment of chips left the factory in a container truck. This had to travel over some high roads to reach the distribution centre. As the truck climbs higher, the air pressure drops. This causes the bags of chips to expand. Because the bags have not been sealed tightly enough, the seal breaks and air gets in to the packet. That is why your chips are stale.
Either way, you are an unhappy customer and have less respect for that brand of potato chip. Bad news for the manufacturer!
Quality assurance
Goods that are transported by air also experience low pressure environments, and so a seal that is too weak could come apart in packages being carried in the hold of an aircraft. Furthermore, this issue is not confined to food products. Medical device companies often seal their products in sterile packs. A weak seal that breaks open unexpectedly could introduce contamination.
Of course, even if the seal strength is correct, leaks can occur if the sealing machine is not set up properly. For example if dust or crumbs have become caught in the heated bar that seals the package.
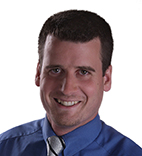
Peter Schlösser
Service Manager
MOCON GmbH |
|
The above examples are given by Peter Schlösser, a packaging analysis expert with MOCON Inc. “In all of these scenarios there has been a quality control problem with the package seal” says Peter.
”In the one case the seal bonding is too tight, in the other not tight enough. To avoid this type of problem you need the right kind of quality assurance procedures on the packaging line to ensure seal integrity”. Read more about quality assurance. |
Leak and seal strength
According to Peter, key aspects of the package quality assurance that need to be considered are:
- Leak test
- Seal strength test
- Such tests must be validated and accepted by the relevant regulatory agencies
”Usefully, technologists working with the packaging industry have developed ways of carrying out these tests with a single device that can be used in different modes,” Peter says.
Seal strength test
”One of the most effective ways to measure seal strength is by using a burst test,” says Peter. Here the operator pierces the package with a hollow needle. This is done through a flexible polymer seal, termed a septum, which ensures that air cannot escape from around the needle. The testing device then pumps air into the package at a precisely controlled rate. As the package inflates the machine records the internal pressure. ”Eventually the seal will fail, and the machine records the pressure at the burst point,” Peter notes. ”The aim is to ensure that the seal bursts within pre-set limits: a low enough pressure to make sure the package can be easily opened, but high enough to ensure that the seal remains intact during transport and handling. This test should comply with the standard ASTM F2054".
Peter remarks: ”If this test had been applied to your potato chips, it is unlikely that you would have had the unfortunate experiences of the impromptu ’chip shower’ or the disappointing stale product!”
Seal integrity
A second test, called a creep test, is a way to test seal integrity. ”Here, the operator uses the needle as above to inject air into the package under a constant pressure for a set amount of time to see if the seal peels open,” Peter explains. The creep test should comply with standard F1140.
Leak test
An effective way to test if a package is leaking is to use a pressure-loss test. Peter says: ”In this test the operator sets the instrument to inflate the package to a pre-determined pressure and leaves it to stand for a time. If the pressure inside the package starts to drop, this indicates that there is a leak. The standard for this test is F2095”.
Leak detection
”If you detect a leak in this way, you can then place the package under water and repeat the test,” notes Peter. ”Bubbles will indicate where the leak is. This bubble test is a good diagnostic method which you can then use to track back to the package sealing unit. It could be that something is preventing a good contact with the heat bar on the sealing unit – crumbs or other contamination, for example. Or maybe the heat sealing unit has an electrical fault”.
Size of leak
In the ’advanced leak test’ mode, the device calculates the size of the leak, based on the flow rate of gas into the package that is needed to maintain a constant pressure. The greater the flow rate needed, the bigger the hole.
Automatic data logging
The more advanced machines capable of carrying out these tests are computer controlled and automatically log all data. ”This is a very useful facility for auditing purposes and for checking the history of testing on a given packaging line,” Peter suggests.
So... happy chip eating
The tests described above will all help to ensure that the seal on your package is as it should be, says Peter. ”The key point is that quality assurance is paramount: when your customer opens a bag of chips to share with a loved one, they do not want an embarrassing accident because it has been sealed too tightly. Or they do not want to give their sweetheart a stale chip. That is not so romantic. Of course this is a light-hearted example, but customers can be unforgiving if their product is sub-standard. So it is worth investing in quality assurance to ensure that the product is right and that the brand’s reputation is not damaged”.